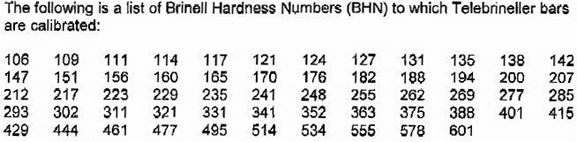
Simple,
Certain Operation under all Conditions
The Telebrineller system is a major achievement in quality assurance. This
system is based on proven metallurgical knowledge supported by more than fifty
years of field experience.
LightWeight: The complete Telebrineller system,
in its case, weighs less than ten pounds. Easily transported to
any location, it is highly practical for all Brinell hardness testing
needs.
Simple Operation: One hammer blow, measurement
of the resulting impressions, and the manipulation of a basic equation
on the computer provided- that's all. No special training required.
In a few minutes, anyone can learn to determine BHN accurately.
Certified Accuracy: The test bars which are the
core of this system are calibrated to a uniform hardness of ±3%
of the labeled BHN. Hardness of the bars is measured by equipment
whose accuracy is certified traceable to the National Standards
Institute. The Telebrineller microscope is by Leica. Readings may
be made within .05 millimeters.
Weatherproof: Designed for field use; there are
no delicate adjustments or fragile components to be concerned with.
All parts are rugged, solid, able to deliver accurate measurements
in all weather, under the roughest field conditions.
The Telebrineller System - Its Principle of
Operation
A test bar of known BHN, approximating the hardness
of the specimen to be tested, is selected. Consistent accuracy
is maintained when the test bar BHN is within 15% of the specimen
BHN and is of the same general material. (Testing non-ferrous materials
with carbon steel bars causes impact errors that must be compensated
for by applying correction factors to the test results.) The test
bar is inserted into the Telebrineller instrument and the instrument
placed upon the specimen.
When the Telebrineller instrument is compete with test bar (1), the anvil (2),
encased in a soft molded rubber head (3), rests on the test bar. The rubber
head and a similar resting block (4), provide non-skid footing. Below the test
bar, a steel impression ball (5), secured in the base of the head, is in contact
with both the test bar and the specimen. The anvil is struck sharply with a
three to five pound hammer. The impact, regardless of force, is transmitted
equally to the test bar and, through the impression ball to the specimen metal
(6), making impressions in both. The diameters of the resulting impressions
are directly related to the respective hardnesses of the test bar and the specimen.
A spacing bar (7), operated by a spring catch and button, adjusts the test
bar to a clear area for each test. By turning the bar to utilize the full length
of all four faces, a total of 80 tests can be made with one bar.
Measuring Diameters: The bar is removed from
the instrument and the Telebrineller Microscope positioned over
the appropriate impression. The microscope provides a scale of
1/10 millimeter divisions and is designed so that the image and
scale are bright and clear to the observer. A numbered division
is aligned tangent to the impression and the diameter measured
by the division that falls over the opposite tangent. Readings
may be made easily and accurately within .05 millimeters. The
impression in the specimen metal is measured in the same manner.
Both measurements take just a few moments.
Determining BHN- The Brinell hardness of the specimen metal is determined quickly
with a simple mathematical equation:
x (BHN of Test Bar) = BHN of specimen metal.

EXAMPLE: Assume the impression diameter of the test
bar is measured to be 3.05; the impression diameter of the specimen
metal, 3.15; and the labeled BHN of the bar is 352.
thus the BHN of
the specimen metal is 330.
This computation is simplified with the use of the
Telebrineller Computer or any pocket calculator. Complete instructions
are included in every Telebrineller system. Telebrineller replacement
parts and test bars of hardnesses from 100 to 600 BHN are always
available.
|